Metalworking in furniture production: it is practical, aesthetic, reasonable
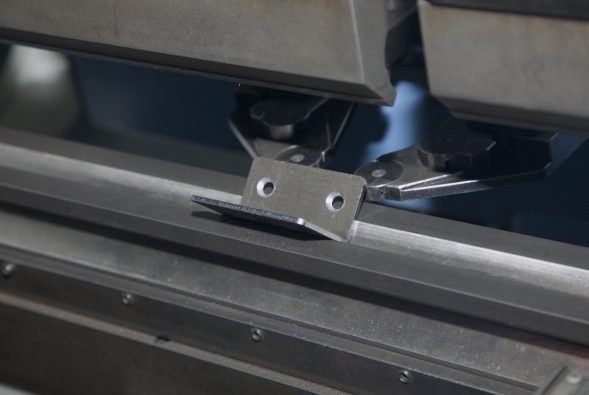
Dmitry Borisovich Demchenko, a leading engineer of Enran CJSC, told Mebelnoe Delo Magazine about metalworking technology.
Metalworking in furniture production: it is practical, aesthetic, reasonable
By opening its own metal processing shop, Enran experts were able not only to integrate different technical solutions but also to improve the production process, which, in turn, was accompanied by a significant extension of the product assortment. The chief engineer of Enran CJSC Dmitry Demchenko told about the peculiarities and difficulties that the engineers had to face, the specifics of using metal in furniture manufacturing, and about the capabilities of this material.
Solid base
It is common belief that furniture is made of wood. However, once the furniture became not only a household article but an original part of the interior architecture, the need for durable and elegant supporting structure arose. It is hard to make such constructions from wood. This is why metal became so popular. Especially for loft style decorative elements, which is all about minimum partitions and maximum open space with furniture that requires solid supports. So-called ‘lacy’ elements, for example, chairs, bed frames, table frames and other usually can’t be done without metal.
It is better to do everything single-handedly
Since 2008 our company made a decision to extend its assortment. We had a clear vision of market requirements thus we started to work with interiors. At that time we already had wide experience of working with different materials like wood, glass, stone etc. at our facilities. But to bring design ideas to life, we needed metal. By that time it turned out that there were no enterprises in Ukraine who could implement our engineering and design solutions regarding metal constructions in one package and within the required term. The process of coordination of construction issues, needs and possibilities of production by different producers required a lot of time. For this reason, we decided to cover with our own resources the wide range of tasks that required the use of metal. When choosing the metal products assortment, we focused on support parts (movable and stationary). Of course we couldn’t forget about fastening details. They always come together with joining elements – fittings. The application range of metal structures in interior is vast. They are office, hotel, sport and entertainment centres solutions. We work in various fields where the use of metal structures in furniture is required. These are various mobile stands, panels, supports, furniture legs – the list of products is very long. In any case, the production has its peculiarities.
Peculiarities
For example, if we are talking about supports, we should consider sheets or pipes of different diameter, mostly round, that require treatment. If the support is made of bent pipes, we need to join them properly. We can bend them mechanically. But the process quite hard. In fact, metal requires careful welding taking into account its physical properties (thickness, firmness etc.) We use ferrous metals (stainless steel) and nonferrous metals. Each metal requires individual approach. For example, thin metal sheet requires arc welding with a non-consumable electrode in a protective inert gas atmosphere. Its a complicated task for a qualified welder. But most importantly, as a result we can get a beautiful seam that may not require additional treatment. Modern tendencies, especially in Europe, take advantage of such technique. The accent is made on the aesthetic qualities of the seam, the delicacy of its performance. At our facilities we use argon arc welding machines Jasic TIG-315p (E103) и TIG-AC/DC MMA-DC . In fact, the welding process can be robotised but unfortunately it’s a quite expensive method intended for serial production.
Equipment
Sure thing, the hands and brains of the expert are very important for metalworking process, especially for milling, turning, bending, welding. In any case everything is done by man. But it turned out that it’s not that easy to find a good mill or lathe operator. Today, educational institutions provide a very few experts in this field. For this reason, we focused on NC machines for cutting both sheet metal and pipes, workpieces milling, metal sheet and pipe bending. We had to learn how to bend pipes (we use NC CNC-65ms 5A bending machine), cut and bend sheets (CNC AP 2600-120 hydraulic sheet bending press), mill (YCM MV 66A milling and processing centre), weld (welding machines with consumable and non-consumable electrode, contact welding machine, stud welding), turn, perform benchwork and painting.
Technological process
The metalworking process starts with workpiece cut using scissors, guillotine, laser or hydro abrasive depending on the material. Next is drilling, benchwork, installation of fastening details, welding and seam cleaning and preparation for painting if necessary. We use a laser for cutting that performs the work with high precision. Especially when it comes to complicated geometric forms or 3D details. Usually, we come across with problems that can’t be solved without laser, particularly in supports. For example, we need to make a special cut on 3 sides of a 4-side shaped pipe and bend it so that the cut line on all 3 sides is closed. This will give us a support of required form. Only 3D-laser can fulfil such task. Our facility is equipped with MAZAK Space Gear MK-II laser cutting machine with a capacity of 1.8kW. Another example. In our Spider series the support is made of 10 mm steel plate covered with wooden overlays. It is very hard to cut such size on milling machine. But it can be done with a laser or hydro abrasive. Plasma cutting is also an option. But in this case fire scales are inevitable. Also, the cut will be uneven, and we want to get a reflecting face of metal insertion. Thus it is laser equipment that can correctly perform all operations.
Preventing defects
Unlike wood, metal is a hard-to-treat material, and it’s not easy to make the desired detail of it. That’s why it is necessary to use certain methods that help to reduce errors. And we’ve learned how to do it. For example, when fixing a detail (edge) that should be welded in vertical position. The thing is that during some operations the detail fixing conductor can shift. In order to avoid this, our experts make special studs in the edge that allows preventing such shifts completely. The surface to which the edge is attached has corresponding cuts for these studs. We start with electronic drawings (assembly and detail), after that the drawings are converted into programmes for NC laser cutting. The cutting is performed according to these programmes with 0.001 mm precision. There is another important aspect. When designing a metal construction we should consider its further production, transportation, assembly and operation. As for the cutting precision, of course there are machines that can cut any detail of any shape using a wire with diamond dusting or electrolytic erosion. We don’t have such thing. Thus we don’t make projects for such products. We should always consider the equipment available at the enterprise. In fact, the whole metalworking process depends on the condition of the material. In Europe, it is still a mystery how even cold-rolled metal, which by all technical parameters implies oil processing, sometimes comes rusty. For this reason, additional cleaning and polish are required.
Mounting peculiarities
As I said, it’s a modern trend to make metal products without additional treatment and cleaning. Apart from fine welding we can use a mechanical mounting. Here we have another interesting technology. When we need to fasten together two pipes, traditionally we use a bolt and a nut. But a nut can bulge out (in case we cant screw it from the inside). Therefore, we can use an anchor or rivet nut. We can also make a bush with internal thread. Another technological option is thermal drilling. There is a special drill that heats up while rotating. It heats the metal making it flexible. This gives us an opening with a skirt. After that the thread is rolled. This technology and tools were designed by Flowdrill company.
Painting
After the welding and joining are done, metal details should be painted. Today, there are many painting compositions. The most exotic one is probably metachrome, or in other words, chemical metallization. We wanted to use this technology at our enterprise but decided to give up this idea due to a number of reasons. This is an alternative to chrome nickel. Besides it is too expensive to cover large areas with this composition, which is inevitable during serial production. Today transparent powder coating is quite popular in the world. That is a natural colour. It is also important that the material is properly welded. The product should have no visible defects since the coating is transparent without any primer or filling of the surface. NC machines allow us to solve technological problems where bench working is not allowed. This is how many European manufacturers work. We meet during various exhibitions, adopt their experience and introduce it in Ukraine.
Design
It is clear that market and its tendencies dictate the demand, but the demand itself can be really versatile. For example, the main trend of German manufacturers if maximal functionality, meanwhile French producers prefer beautiful fancy shapes. Loft style is also very popular on the West but is quite new for Ukraine. We have to be ready to use its advantages. However, the customers’ requests are quite original today. For example, if welded seams in new furniture products are not cleaned but covered with enamel, and over the enamel, a thick paint is applied with a brush. It’s a true disaster for a professional. However, this technology of surface treatment is very popular in Europe, since the customers like this designer solution. Once, our company made a series of works for European customers. One of the products had to have 592,2 mm measurements. This accuracy is beyond furniture products. We were allowed a two tenths deviation. We had to solve the task, and we made a large batch of products with such deviations in measurements. Eco-friendly materials is a top trend today. Ergonomics and noise protection are also important, especially for offices. Open space is still in the lead. Therefore, noise-absorbing panels, free, spacious communication areas are very important, as well as the use of various technical devices for lifting tables, the illusion of subtlety, airiness, elegance and at the same time functionality. For example, long conference table with lots of metal supports is nothing special. Modern interior design prefers concrete and metal, but without rusty colour. Rolled metal usually has glaucescent shade. In Enran we apply transparent powder coating on metal constructions to receive original required colour. However, neat seams is the most important part. In my opinion the use of metal in furniture production and interior design is justified by its functionality and aesthetic features. This is what global market wants today.